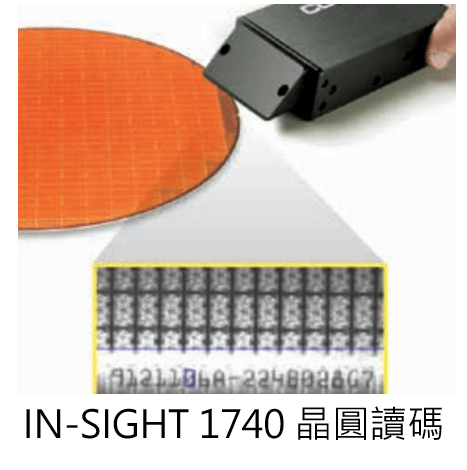
半導體解決方案
積體電路晶片的可追溯性要從製造層級開始。識別與可追溯性代表讀取晶圓 OCR 碼,有時也代表讀取 IC 封裝 DataMatrix 碼。此領域的新趨勢為在晶圓背面標上多個標記,以及提供晶片尺寸的可追溯性。晶圓、晶圓載具、引線架構、晶粒及成品封裝都會有識別條碼,必須在製程的每個步驟讀取和驗證。
自動識別以進行晶圓追蹤
康耐視晶圓 ID 系統已樹立了高讀率和穩定可靠的標準,In-Sight 1740 系列也不例外。In-Sight 1740 系列晶圓讀碼器麻雀雖小、五臟俱全,能發揮極致效能!一個完全獨立運作的小巧系統,提供了達成高讀率的一切功能,且依然穩定可靠。
半導體對位解決方案 In-Sight 1740系列
半導體製程需要超高精確度。多年來,晶粒密度持續地穩定增加。現今的半導體特徵為奈米級的尺寸大小,在進行光刻、切割、引線接合及封裝等製程時,需要超高精確度與對位。康耐視對位解決方案使用領先業界的機器視覺工具,即使在條件不利的情況下,也能迅速又精準地找到和對準圖案與基準點,能協助達到最高產能、改善品質及降低成本。
晶圓 Notch 定位- In Sight 1740/1741/1742
面臨的挑戰
在晶圓處理流程期間,半導體晶圓的位置與方向至關重要。做法是監視晶圓上的 Notch,藉此瞭解每個步驟的晶圓方向。在處理流程期間發生任何錯位,都會導致嚴重且無可挽救的缺陷,而必須將晶圓報廢。
尋找 Notch 的傳統方法使用對照式陣列鐳射光學件配置感測器,其需要在晶圓上方與下方放置龐大的發射機與接收機。這會佔去 寶貴的機械空間,還會增加旋轉晶圓直到找到 Notch 的時間。引進透明晶圓 (SiC) 與其他獨特的晶圓塗層,使得對照式感測器難以 精準地找到 Notch,而增加在特定流程期間發生錯位的機會。
解決方案
康耐視 In-Sight® 視覺系統能以低於 0.025 圖元的精準度,精準地識別晶圓的 Notch 與 XY 位置。不論晶圓的 Notch 朝向何方,康耐視的 PatMax® 圖案式物件定位技術都能精準地探測,並將位置與尺寸資料輸出,送回裝配機器人或可程式設計邏輯 控制器 (PLC)。此外,視覺系統超小巧的機體設計可滿足極小 的體積限制,完全不需要在晶圓上方與下方放置鐳射光學件配置感測器。康耐視也有專利的低輪廓光學件配置系統,可在製造廠商無法在較遠的檢測距離裝設鏡頭時,用以檢視整個晶圓。
晶圓和晶粒對準- In Sight 1740/1741/1742
面臨的挑戰
無論是在光刻處理、晶圓探測和測試或晶圓安裝和切割期間,視覺對位不良會讓機器使用壽命內需要的協助次數與產生的損壞 晶圓數,達到成千上萬。執行性能不佳的視覺系統會使半導體設備公司失去市場占有率,並大幅增加其支援成本。
解決方案
PatMax 技術能穩健、精準又迅速地定位圖案,進行晶 圓檢測、探測、裝設、切割及測試装置,協助避免發生問 題。PatMax 使用專利的幾何圖案定位演算法,尋找和對準 各種不同的晶圓與晶粒圖案。高度精確且一貫的晶圓與晶 粒對準能力,確保半導體製造流程的全程都有可靠的設備 性能。與康耐視合作,OEM 能讓其設備的整體性能達到最 佳狀態,改善品質與產能。
晶圓OCR- In Sight 1740/1741/1742
面臨的挑戰
晶圓的 ID 號碼會以鐳射標記在矽碟的一小塊區域。這些條碼不是英數字 元,就是 DataMatrix 碼,並可在晶圓切割之前,用來在前端製程期間全程 追蹤晶圓。歷經不同的光罩、刻蝕及光刻製程後,晶圓 ID 可能會劣化,在晶圓的反光背景下變得難以解碼。
解決方案
康耐視 In-Sight 1740 系列晶圓讀碼器採用專為晶圓識別開發的先進演 算法,在切割晶圓之前,提供光學字元辨識 (OCR) 與二維讀碼功能。這些 晶圓讀碼器使用適合的集成光源與圖像處理功能,可為各種不同的標記 方法提供最佳的成像系統,包括英數與 SEMI-T7 DataMatrix 碼。In-Sight 1740 能自動順應因不同處理步驟造成的標記外觀變化,因此可減少無法 讀到資料的情況,幾乎無需進行機器協助,並使機器運轉時間達到最長。
晶粒表面缺陷檢驗- In Sight 1740/1741/1742
面臨的挑戰
在積體電路製造流程中,務必檢測每個晶粒,檢查表面是否有裂縫、碎裂、焦痕等,因為這些缺陷會對晶粒的品質與性能造成負面影響。這些缺陷不僅樣態多變,而且會出現在不同的位置,對於基於規則的機器視覺而言,要及時準確地找出這些缺陷並非易事。由於也會出現不影響晶片品質的正常像差,因此重要的是不將時間耗費在標記這些微小缺陷上。考慮到每日處理的晶片尺寸與數量,以人工檢測不但沒有效率,也不切實際。此外,減少人工介入,可以降低汙染物進入無塵室的機會。
解決方案
Cognex Deep Learning 的缺陷探測工具可在晶粒表面上找到不可接受且樣態眾多的塗裝缺陷,但對於基於規則的視覺檢測系統 而言,卻是過於複雜或相當費時。該工具會檢查晶粒的表面,檢測各處是否混合出現任何裂縫、碎裂或焦痕。利用可展現缺陷類型與位置變化的許多不同圖像來訓練軟體。識別出潛在的目標檢測區之後,再由 Cognex Deep Learning 的分類工具將缺陷 (例如,裂 縫、碎裂、塵斑等) 分類。使用這項資訊,可以改善流程以減少缺陷並提高成品率。
檢查焊線是否有缺陷- In Sight 1740/1741/1742
面臨的挑戰
在許多積體電路與微晶片內,最常用來相互連線的方式就是使用引線接合。這是需要高準確度的精密流程。引線接合的目的是,使用極細的金屬線,將晶片上的引線連接至封裝材料。封裝材料可以將訊號傳輸到其他組件。像是引線斷裂或遺失等缺陷,都會造成訊號 中斷傳輸。這些缺陷可能有許多不同的類型與出現位置,更是讓基於規則的機器視覺解決方案難以準確地判斷有缺陷的引線接合。
解決方案
傳統上,搭配基於規則的視覺統使用自動光學檢測 (AOI) 系統無法運作良好。透過深度學習檢測疑似不良 (NG) 的情況,可強化檢測 流程的可靠性。AOI 機器會使用 Cognex Deep Learning 工具,挑出疑似 NG 的情況並將圖像提供給系統。缺陷探測工具可動態擷 取目標檢測區,而分類工具可將不同的缺陷分類,區分有缺陷與可接受的引線接合。將缺陷分類,不僅有助於發現流程中的問題,避免在生產線下游進行所費不貲的重工,同時還可成功識別微米級的缺陷,改善 IC 晶片成品率與壽命表現。
面臨的挑戰
晶圓切割之後,便無法再使用晶圓 ID。為了讓先前在晶圓上產生的晶粒保有可追溯性,都會使用標有識別號碼的載環輸送切割好的矽晶圓,直到從載環取下以進行引線接合為止。切割製程會讓鋸開時產生的碎片四散在晶粒與載環各處,因此必須清理乾淨。重複加以清潔會讓載環的表面劣化,而降低條碼的可讀性。
長時間下來,表面與字元樣態會出現繁多變化,使得基於規則的視覺技術難 以準確地讀取這些條碼。如有淡化或磨損的情況,想要區分像是 0 與 O 或 l 與 1 的字元,並不是一件容易的事。條碼無法讀取的載環 會拖慢自動化流程的速度,進而影響產能。使用 OCR 讀取晶圓載環上的條碼,不僅可延長其使用壽命,並能保持自動化流程不間斷。
解決方案
即使晶圓載環上的識別條碼因多次清潔而劣化,Cognex Deep Learning 工具還是能讓製造廠商精準地讀碼。結合智慧相機與深度學習軟體一起使用,運用光學字元辨識 (OCR) 將受損的條碼解碼。由於有深度學習預先訓練的字型庫,軟體內的深度學習讀碼工具 開箱即可使用,大幅縮短開發時間。使用者只需要定義目標檢測區,並設定字元大小即可。引進新字元時,不必具備視覺專業知識,也可以重新訓練這項穩健的工具,讀取傳統 OCR 工具無法解碼的應用特有條碼。
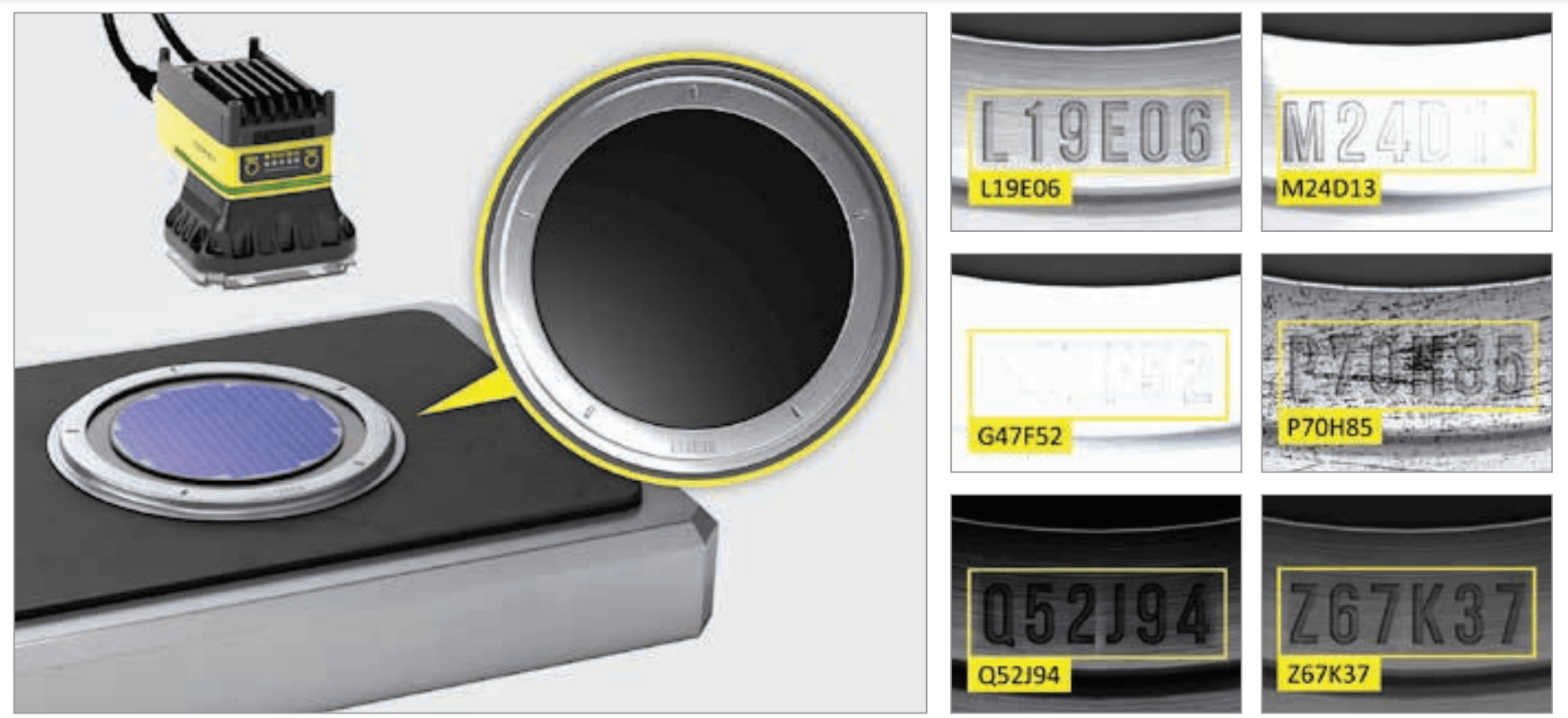
積體電路封裝可追溯性- IN SIGHT 1740/1741/1742
面臨的挑戰
引線架構為一層薄薄的金屬,可將接線從半導體表面上的電氣端子連接至電子產品裝置或電路板上的大型電路。晶片會以引線接合至該引線架構的金屬引線。二維 DataMatrix 條碼經常以鐳射刻劃在每個引線架構上,以便在整個裝配與製程期間追蹤引線與晶片。由於這些條碼會在生產期間劣化,還具有低對比且反光的金屬背景,使得讀碼的難度極高。
解決方案
康耐視 DataMan® 圖像式讀碼器配備引先業界的演算法與防靜電防護外殼,即使在最嚴峻的條件下,也能可靠地讀取二維 DataMatrix 碼。靈活的光源與光學件配置可提供最清晰的圖像與最高的讀取率,禁得起許多安裝與照明限制。已在可追溯性應用之 中成為標準的 DataMatrix 技術,可儲存關於引線架構的所有必要資訊,例如製造廠商、產品編碼、批號,甚至是不重複的唯一序號, 確保有高效率的可追溯性。
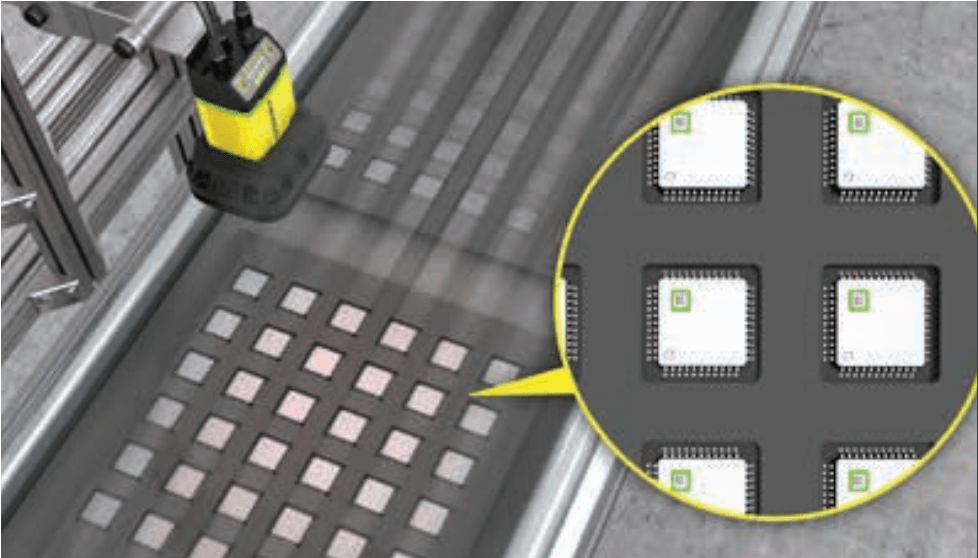
讀取IC上的字元與條碼- IN SIGHT 1740/1741/1742
面臨的挑戰
完成封裝測試流程之後,半導體晶片終於取得其識別號碼,當中包含了製造廠商資訊與 IC 的技術規格。此英數條碼會模壓在 IC 上面。半導體製造廠商能否提供內部與外部可追溯性的關鍵,在於這項資訊的可讀性。系統設計外殼與電路板裝配公司等下游各方,都是讀取這些條碼來驗證所收到的晶片,還有裝在 PCB 上的晶片全都正確無誤。傳統做法是透過由基於規則的機器視覺來識別 和確認這項資訊。
不過,傳統演算法很難讀取以鐳射標記或化學刻蝕在 IC 上,文字極小且變化繁多的字串。其他會影響可讀性的問 題,還有相當粗糙的表面,以及會讓字元在圖像中變形的環境層壓。
解決方案
無法以基於規則的圖像處理技術來解決的各式難題,使用 Cognex Deep Learning 技術都能迎刃而解。Cognex Deep Learning OCR 工具能使用預先以一千個字元訓練的內建字型庫,讀取曲面字串、低對比字元,以及變形、歪斜及蝕刻不良的條碼。OCR 工具 也提供重新訓練功能,讓使用者得以解決無法在第一回合自動識別的全新或特定字元。迅速又準確地讀取晶片的識別號碼,不僅可 改善可追溯性,還可確保擷取到正確的資訊,以在未來需要時提供。
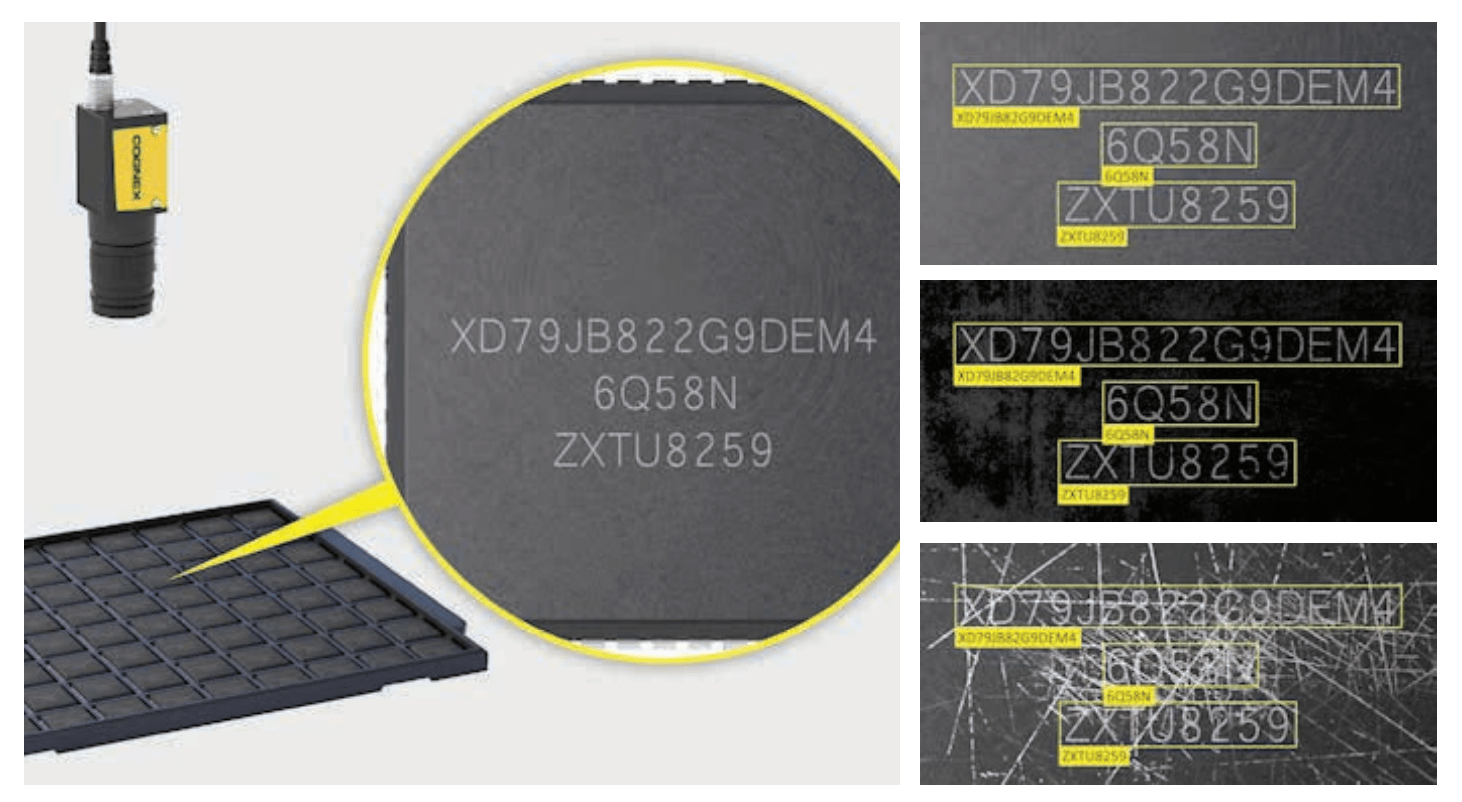
面臨的挑戰
半導體晶圓包含多層構造。每一層都會經過複雜且精確的材料沉積、光阻塗佈、平版印刷、刻蝕,以及在去除光阻之後植入離子的流程。新蝕刻與植入層必須先檢測是否含有缺陷,然後才能繼續加上另一層。晶圓層會顯示刮痕、旋轉缺陷、曝光問題、微粒汙染、熱點、 晶圓邊線瑕疵,還有會影響最終晶片效能的各種不同其他缺陷。
如果未能在晶圓層沉積後立即探測出來,則只有在最終測試時才能發現這類缺陷,因此會對有瑕疵的產品加上額外的價值,而浪 費寶貴資源。更糟的是,可能完全無法發現最低微的缺陷。即使通過最終的電氣測試,未能發現的瑕疵還是可能會降低使用上的 可靠性,並造成過早故障。
可能的缺陷領域廣泛多樣,並可能位於圓形晶圓上的任意位置。塗層中的缺陷本身會以無法預測的色彩變化顯現,因此務必要在 先前所沉積晶圓層的複雜背景上,探測出這類缺陷。傳統機器視覺無法設計程式,探測這類樣態眾多的錯誤,即使已設計程式探測 多層背景上的缺陷也不可靠。
解決方案
半導體產業的特點是要求的品質標準極高,還會快速引進新技術。對於半導體製造廠商而言,測量品質的最佳指標就是「每晶圓 的成品率」。成品率越高,表示獲利率越高。使用機器視覺與深度學習技術,在不同的處理點進行缺陷檢驗,有助於及早識別問 題。
Cognex Deep Learning 技術有助於找出在製造期間造成缺陷的原因,還能迅速採取修正行動和記錄結果。這項技術可以同時忽略落入可接受範圍內的自然變化。隨著將製造流程不斷精進且缺陷數下降,成品率也隨之提高。因為人工檢測速度緩慢,只能針對晶圓 的統計子集執行。其也會導致需要進 行額外的晶圓處理,而引進新的污染 與損壞來源。
相較之下,Cognex Deep Learning 軟體可針對更大部分的晶圓執行自動化缺陷篩選。其也可用於兩層 式檢測系統,識別模棱兩可的情況,以及送到離線人工檢測站,以供進一步閱。
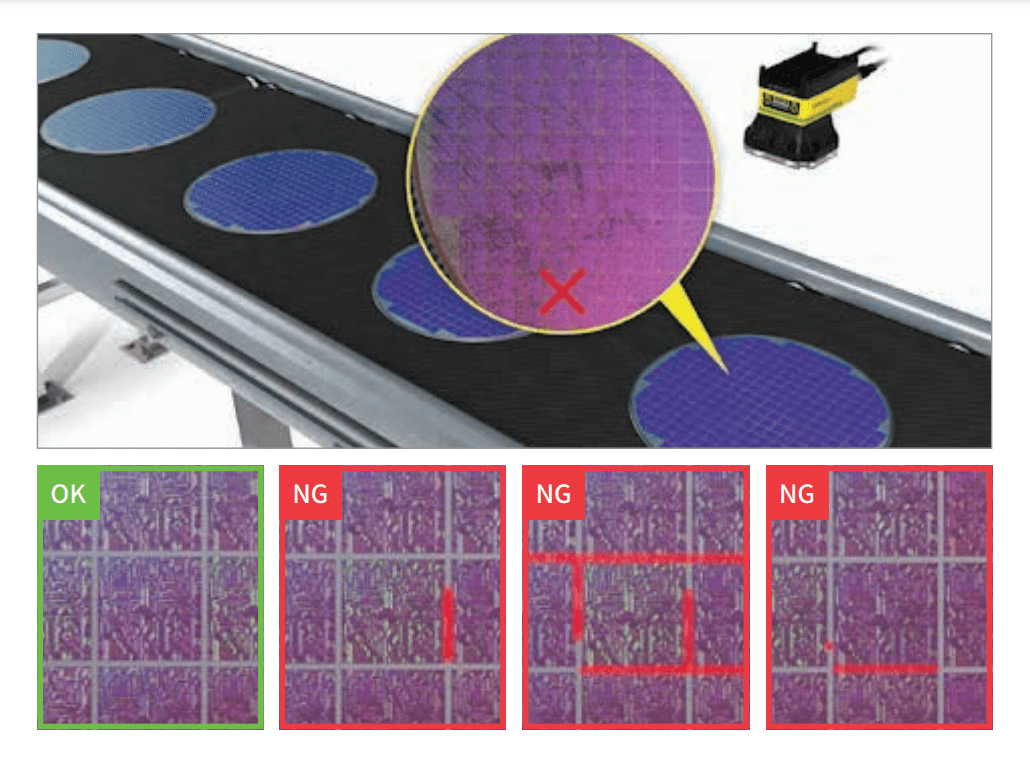
檢測和分類探針標記- IN SIGHT 1740/1741/1742
面臨的挑戰
在將晶圓送往進行晶粒準備之前,都會測試所有個別的積體電路是否有連續性與功能方面的缺陷。此流程會使用含有數十支顯微電子探針的探針卡。每支探針都會在與晶粒接觸時,於上面留下微小標記。此標記應要位於晶粒中央,並指出探針施加了正確的壓力。探針標記是針測機性能是否準確的指標。如果針測機運作正常,就會留下良好的探針標記形狀。如果探針運作不當,就會留下不良 (NG) 的探針標記形狀。
例如,探針施加的壓力若過重,長時間下來就會損壞,而無法執行可接受的電氣測試。 探針本身所費不貲,因此務必要維持正確的壓力,才能延續其工作壽命。因為標記的形狀、尺寸及位置變化繁多,要使用傳統機器視 覺來探測和分類 OK 與 NG 標記並不容易。探測結果不一致或誤讀為不良 (NG),都會對成品率與晶片品質造成負面影響。
解決方案
Cognex Deep Learning 工具可協助驗證 OK 與 NG 探針標記之間的差異,能夠以更短的時間,更輕鬆地進行晶圓檢測。 軟體用以進行訓練的圖像廣泛多樣,包括顯示正確探針標記的圖像與顯示不可接受探針標記的圖像。隨後即可將不可接受的標記分 類為「壓力相關」或「偏離中央」。
作業人員可使用這項資訊,調整探針壓力或對位,以增加可接受探針標記的數量,並讓探針處於良好工作狀態。相較於會將 OK 標記 描繪為不可接受,或將 NG 標記視為可接受的其他方法,針對探針標記使用深度學習檢測,可以提高晶圓的晶粒成品率。
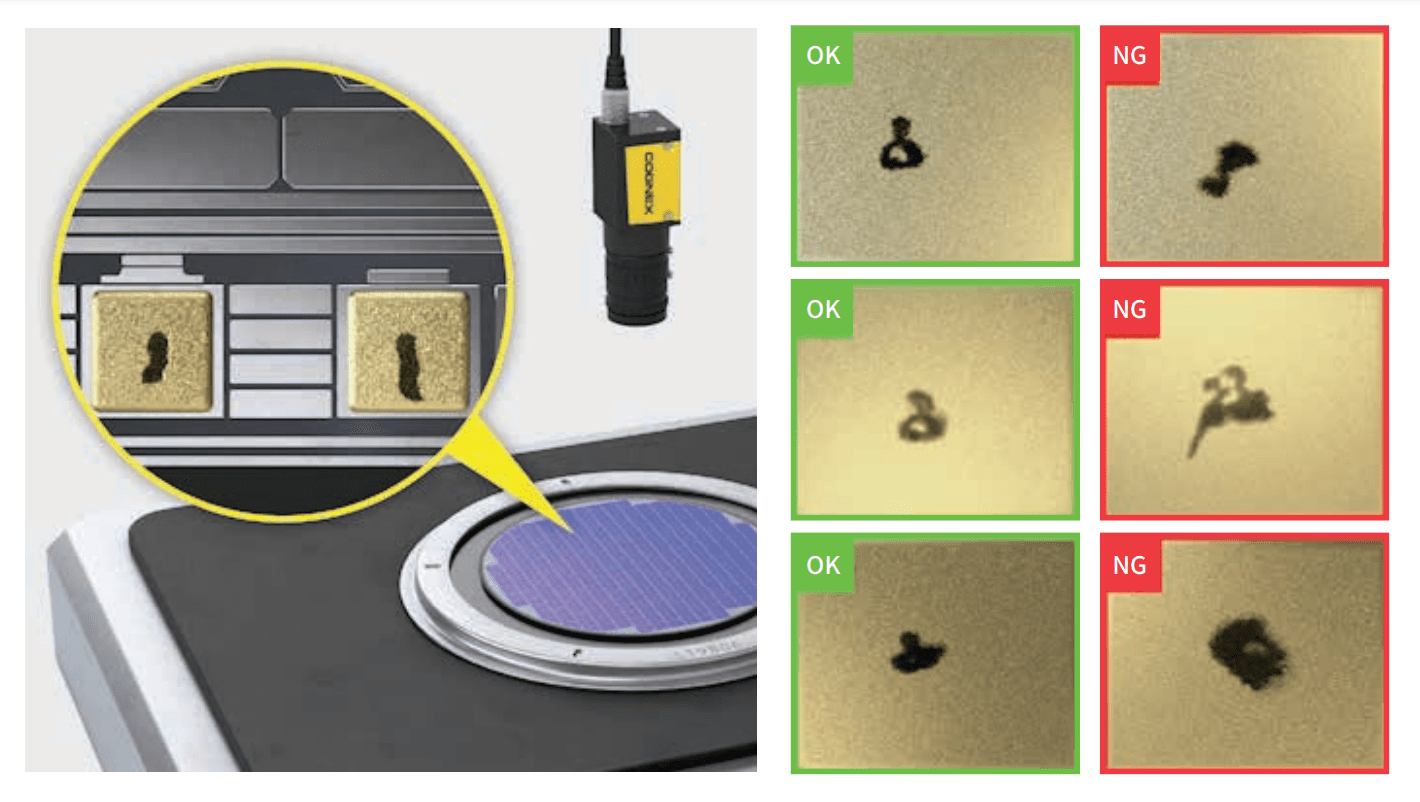
在切割後探測邊緣碎裂或毛邊- IN SIGHT 1740/1741/1742
面臨的挑戰
晶圓會在經過多項不同的層疊與蝕刻流程之後,切割成個別的晶粒。完成此程序之後的晶粒切口沿線可能會留有碎裂或毛邊痕跡。碎裂與毛邊都會影響 IC 裝置品質,因此務必要在切割完成後檢測出來。超出誤差範圍的碎裂處若高於平均數,也表示可能需要調整 或更換切割鋸片。
檢測晶粒的常見方式為使用基於規則的機器視覺,但這種方法通常不夠可靠,因為碎裂與毛邊痕跡的樣態多變,也很難與正常的切 割痕跡或 IC 圖案區分。開發機器視覺演算法,以涵蓋所有變化並區分不可接受的痕跡與在誤差範圍內的痕跡,並非易事。
解決方案
Cognex Deep Learning 工具提供更簡單的方式,來學習和分類碎裂與毛邊痕跡,以及與切割流程後的正常切口痕跡區分。輕鬆訓練軟體,識別所有碎裂與毛邊,分類為可接受或不可接受,以及忽略在誤差範圍內的正常痕跡。製造廠商可以使用這項資訊精進切割流程,例如替換已變得不夠鋒利或太寬的鑽石鋸片。適當探測 OK 與不良 (NG) 之間差異的另一項優點,就是挽救可能因為誤讀而遭到丟棄的良好晶片,進而提高成品率。
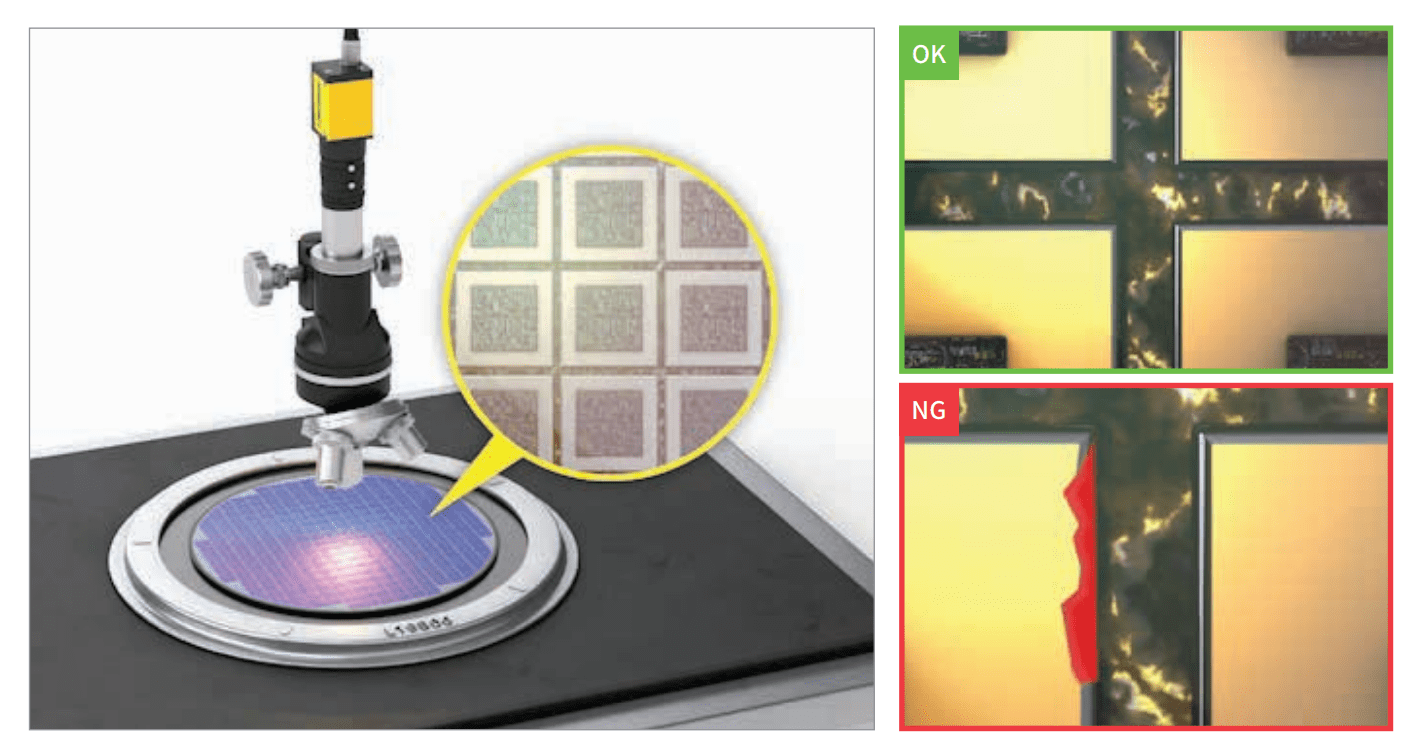